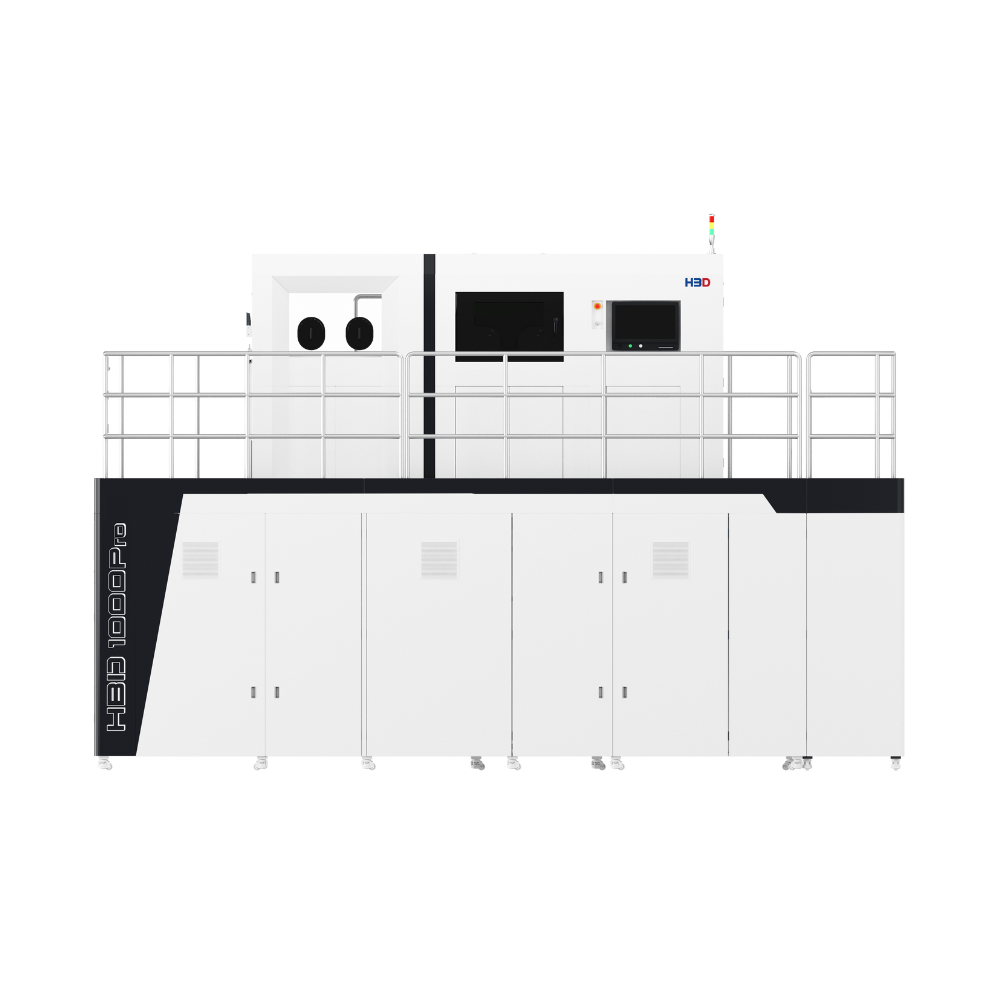
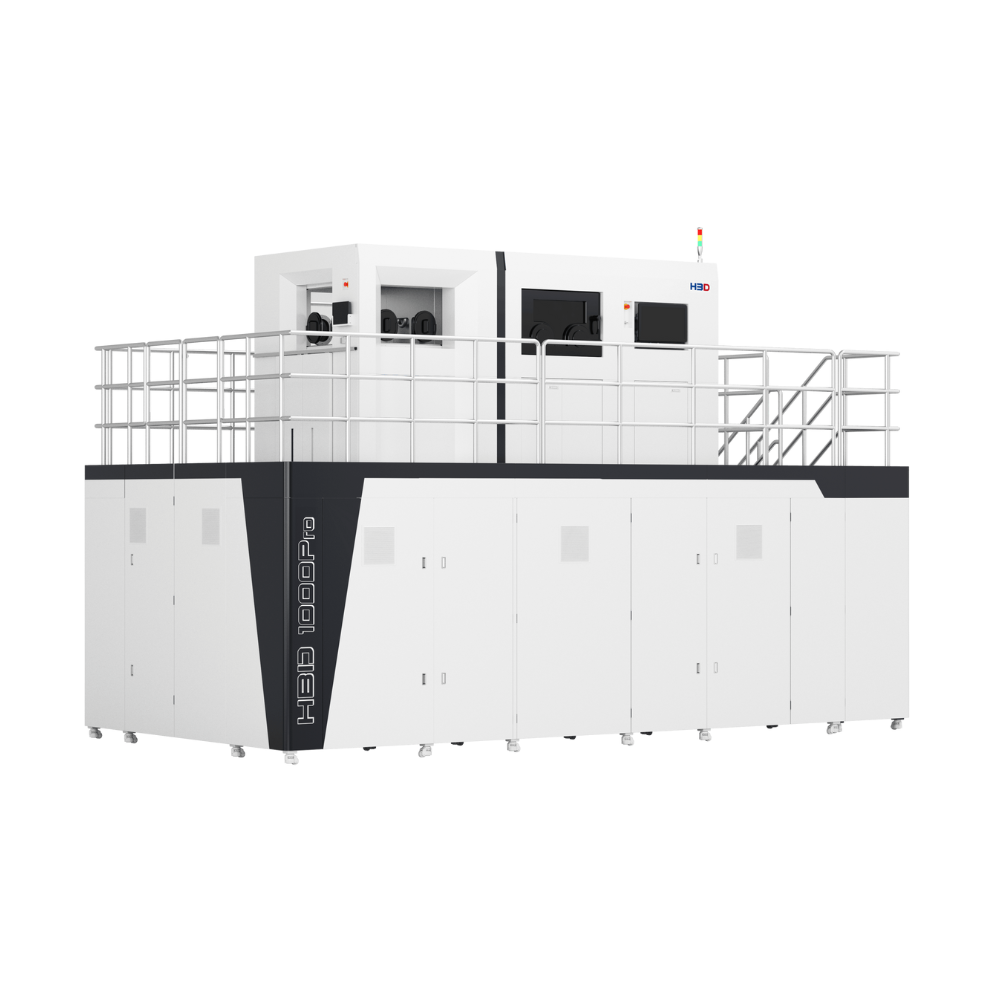
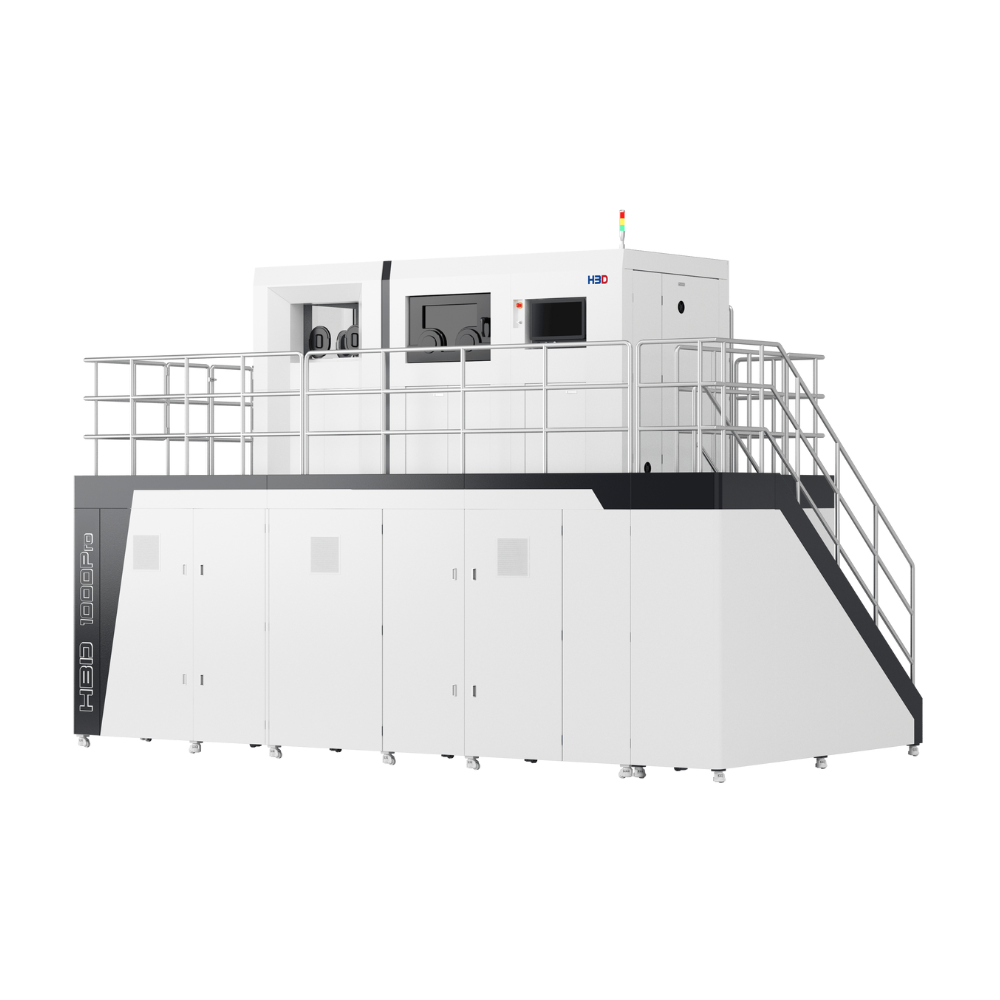
HBD 1000Pro
Built for Extreme Applications
As the largest model in the series, the HBD 1000Pro provides an advanced manufacturing solution for businesses. This metal 3D printer offers real-time powder monitoring to ensure consistent material quality and features 8-laser seam integration for precise results.
Complementary Equipment and Accessories
Based on your request, the solution package includes the following:
Explosion-Proof Cleaner, Nitrogen Generator, Multi-Purpose Forklift, Powder Drying Oven, Powder Suction Machine, Powder Sieving Machine, Wire-Cutting EDM Machine, Vacuum-Atmosphere Heat Treatment Furnace, Sandblasting Station
Materials: HBD series metal 3D printers are offered with parameters customized for the metal powder of your choice.
LPBF (Laser Powder Bed Fusion)
Metal Powders (Metals)
Product Specifications
Download the technical datasheet for HBD 1000Pro metal 3D printer.
Download DatasheetLPBF (Laser Powder Bed Fusion)—also known as SLM (Selective Laser Melting)
660 x 660 x 1,250 mm
8 x 500 W (IPG), 8 x 1000 W (IPG)
±0.05-0.20 mm
20-120 μm
70-200 μm
≤10,000 mm/s
≤100 ppm
Fully sealed system with automatic oxygen content monitoring, powder recycling, cleaning, and collection efficiency of ≥99%.
≥99.90%
Yes
Yes
Yes
500 W Laser: AC 380 V, 50/60 Hz, Maximum: ≤35.0 kW, Average: ≤25.0 kW
1000 W Laser: AC 380 V, 50/60 Hz, Maximum: ≤40.0 kW, Average: ≤30.0 kW
7,050 mm × 3,630 mm × 4,480 mm
16,000 kg
Yes

HBD is recognized globally for developing and manufacturing LPBF systems, with over 200 patents, prestigious certifications, and over 15 years of experience, having served 1000+ businesses in over 25 countries. This expertise and application know-how allow for better customer service, enabling the development of custom and cost-effective solutions for businesses in a variety of industries.

The research center of HBD hosts over 50 industrial metal additive manufacturing systems, all dedicated to application development and creating optimized parameters for third-party materials, testing hundreds of materials each month. This ensures maximized compatibility with third-party materials, allowing customers to achieve success with their applications using the materials suitable for them.
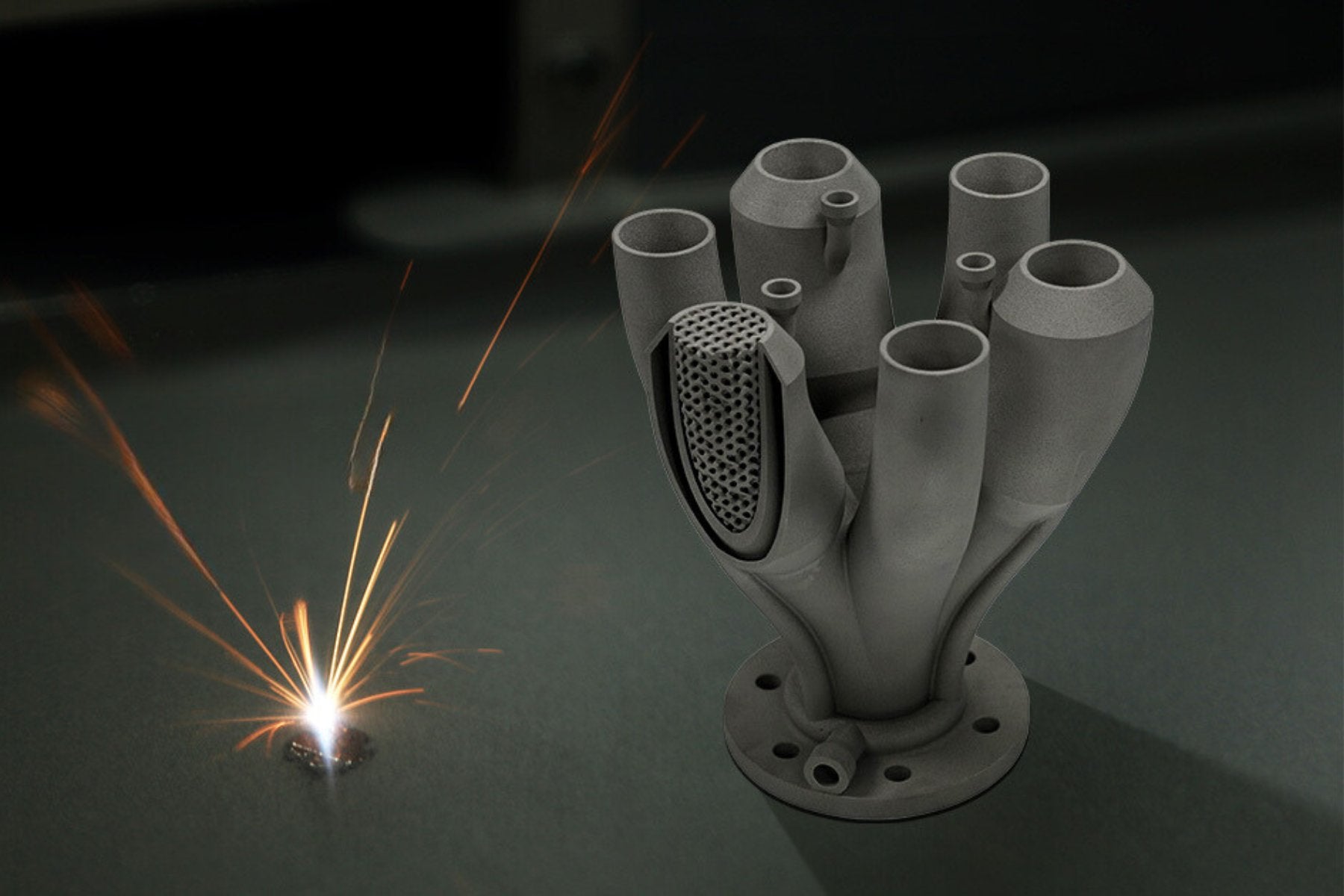
HBD systems offer a monitored manufacturing process. The integral sealed, automatic monitoring of oxygen content, and recycling with a cleaning and collection coefficient over 99% coupled with a closed-loop system, allow for stable and repeatable outcomes. The result is a printing system that can operate continuously for extended periods, delivering reliable production performance.
HBD is recognized globally for developing and manufacturing LPBF systems, with over 200 patents, prestigious certifications, and over 15 years of experience, having served 1000+ businesses in over 25 countries. This expertise and application know-how allow for better customer service, enabling the development of custom and cost-effective solutions for businesses in a variety of industries.
The research center of HBD hosts over 50 industrial metal additive manufacturing systems, all dedicated to application development and creating optimized parameters for third-party materials, testing hundreds of materials each month. This ensures maximized compatibility with third-party materials, allowing customers to achieve success with their applications using the materials suitable for them.
HBD systems offer a monitored manufacturing process. The integral sealed, automatic monitoring of oxygen content, and recycling with a cleaning and collection coefficient over 99% coupled with a closed-loop system, allow for stable and repeatable outcomes. The result is a printing system that can operate continuously for extended periods, delivering reliable production performance.


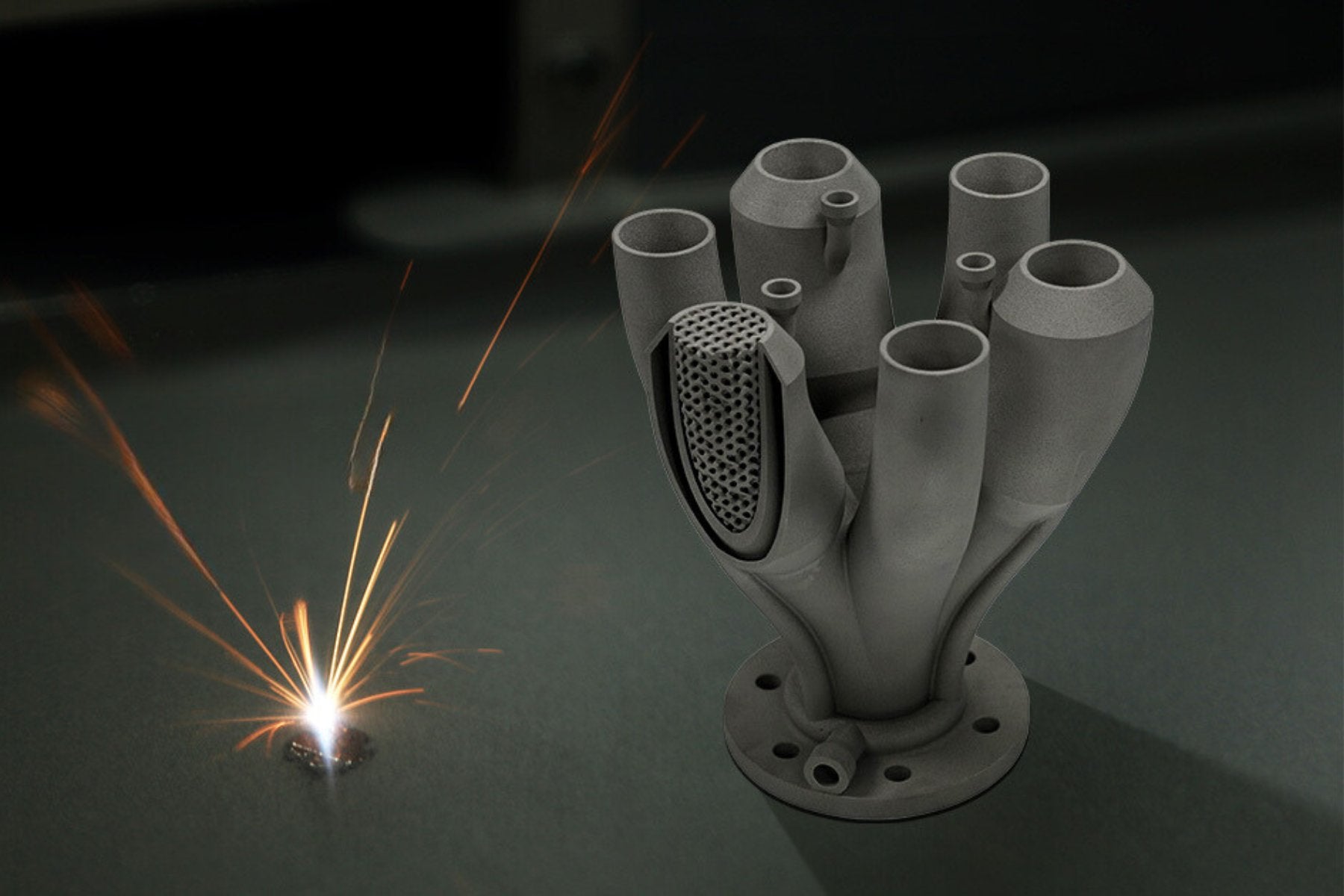
Disruptive Applications
The layer-by-layer fabrication of parts allow for the creation of parts with complex geometries that would be difficult or impossible to produce with casting or machining.
Hydraulic Manifold
Metal additive manufacturing allows for the consolidation of multiple parts into a single, complex hydraulic manifold, enhancing flow characteristics while reducing size, weight, and assembly time.
Conformal Cooling
In the production of molds and inserts, metal AM enables the integration of conformal cooling channels that closely follow the contours of the mold cavity, resulting in more uniform cooling, reduced cycle times, and consistently higher quality in final products.
Heat Exchanger
Maximizing the surface area is essential for heat exchanger efficiency, and metal AM supports this by allowing the creation of highly-complex internal geometries that significantly increase the surface area, thereby enhancing heat transfer capabilities.
Trusted by
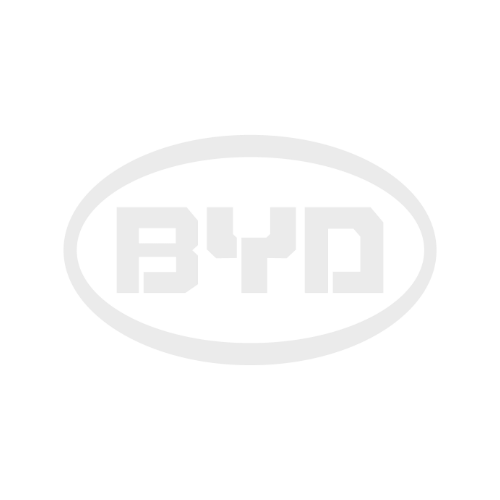

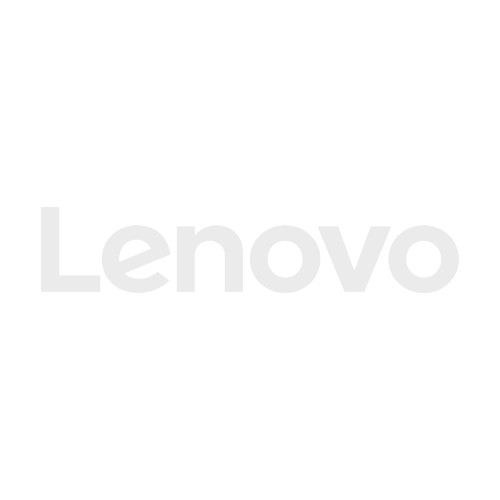
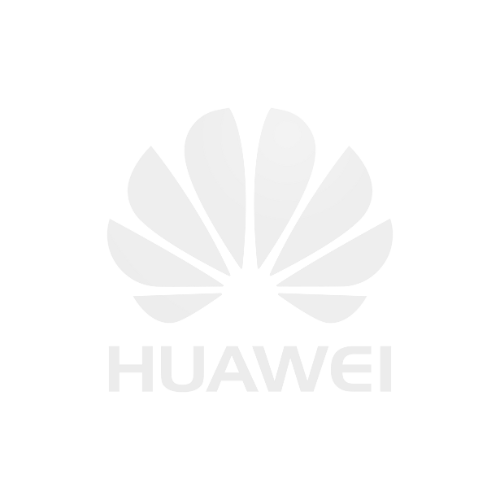

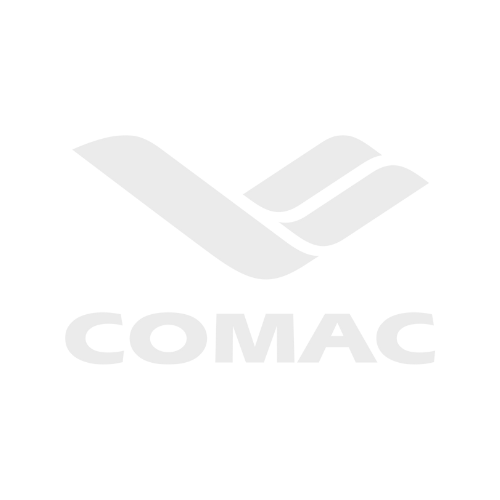
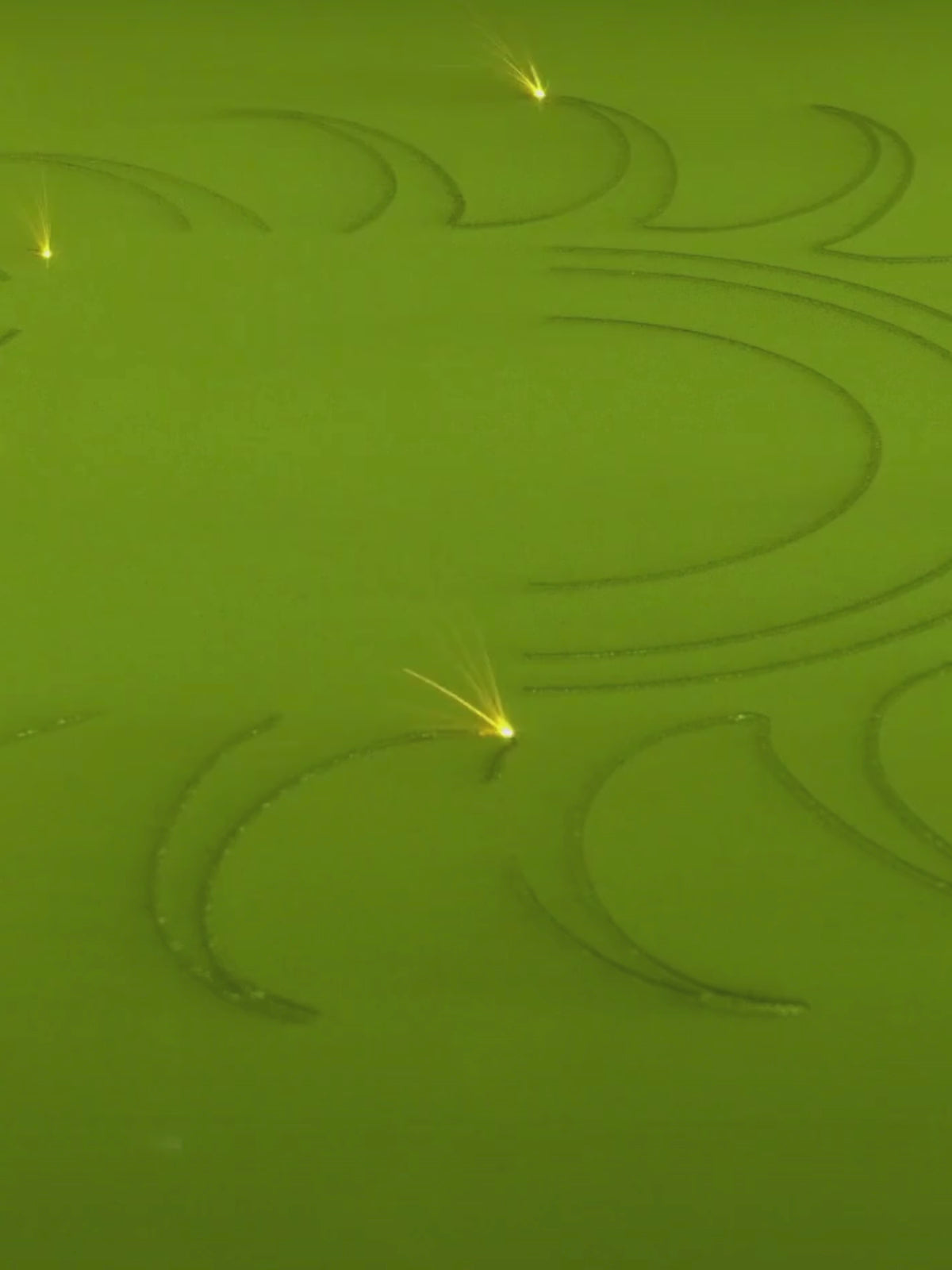
Driving Innovation
LPBF uses lasers to fully melt each layer into the previous one, resulting in completely dense, end-use quality metal parts. CAD files are converted into individual vectors that the laser follows during each layer's exposure, providing businesses with the power of design freedom.
HBD 1000Pro
Feature Highlights
With high production capacity and equipped with 8 lasers, the HPD 1000Pro features a forming size of 660 x 660 x 1,250 mm. It is suitable for large-scale applications such as thrust chambers, impellers, helix radiators, heat exchangers, and aerospace engines.
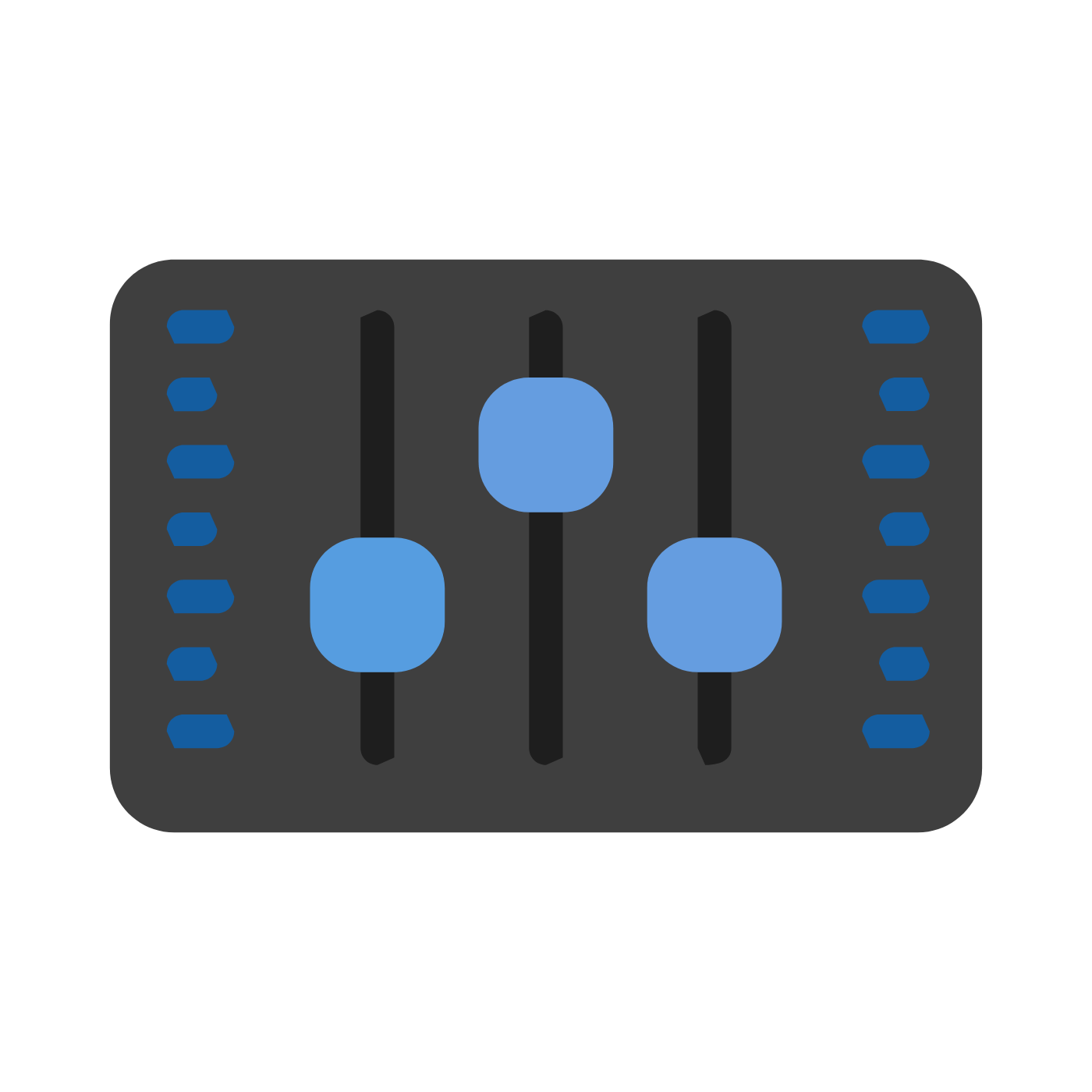
Customizable Parameters
Customizable parameters and a vast library of proven parameters for third-party materials provided by HBD mean a manufacturing solution that adapts to your business's needs.
System Stability
HBD 1000Pro's sub-vacuum sealed chamber, closed-loop air circulation, and high-speed deoxygenation system ensure utmost precision and safety.
Pressure sensors, oxygen detection, and comprehensive safety measures guarantee stable and secure operation. The innovative powder recycler enhances powder usage, optimizing results.
High-Speed Production
Bidirectional recoating, octuple laser configuration, and scanning speeds of 10,000 mm/s allow for the rapid production of complex parts in days.
Superior Print Quality
Customizable for IPG lasers of various powers, HBD 3D printers offer dimensional accuracy down to ±0.05 mm for intricate applications.
The advanced gas flow structure effectively eliminates smoke and splatter, ensuring uniform consistency in large-format printed parts. The high-quality beam (M2 ≤ 1.1) and seamless alignment guarantee forming accuracy and mechanical performance of printed parts.
Bidirectional Recoating and Intelligent Monitoring
Bidirectional recoating in LPBF printers streamlines the application of new powder layers by allowing the recoater to spread powder in both directions, reducing the overall build time and enhancing the efficiency of the printing process.
This not only speeds up production but also minimizes disruptions to the powder bed, leading to smoother surfaces and more consistent part quality.
HBD 1000Pro also features an intelligent powder recoating monitoring system equipped with sensors to ensure precise and efficient powder distribution.
Full-Field Laser Overlap
HBD 1000Pro's full-field laser overlap ensures uniform laser coverage across the build plate, enhancing material consistency and mechanical properties while reducing porosity and defects.
This feature optimizes material usage and speeds up production, making it essential for high-performance industries like aerospace and automotive.
Independent Atmospheric Purification System
Equipped with an efficient and secure independent atmospheric purification system to ensure highly efficient purification during the printing process, providing a safe and stable solution for printing reactive metals.
It also features an automatic closed-loop purification circulation system with advanced dust removal and secondary filtration. These enhancements ensure high filtration efficiency, meeting H13 standards.
Sealed Operating Environment
Adopting a sealed glove structure, a sealed chamber is reserved for the powder adding and suction interface, which can be operated without opening the chamber for powder adding and powder clearing.
Long-Lasting Filtration
The filtration system features next-generation PTFE-coated filter elements that meet H13 standards.
The self-cleaning capability extends the filter element’s lifespan to over 5 years. An optimized gas-flow configuration ensures secure and efficient waste reclamation in inert gas environments, maintaining ideal printing conditions.
Upgraded Marble Structure
Designed with an marble internal structure, the HBD 1000Pro provides enhanced long-term stability and printing accuracy.
Intelligent Management System
The built-in industrial-grade camera monitors powder coating quality and intelligently handles various abnormal situations. The optional thermal imaging online monitoring module detects temperatures in real-time at different positions in the printing slot, optimizing printing process parameters.
The HBD AMES intelligent management system integrates the HBD System equipment control and HBD Build Expert path planning software, offering open parameters and customized services.
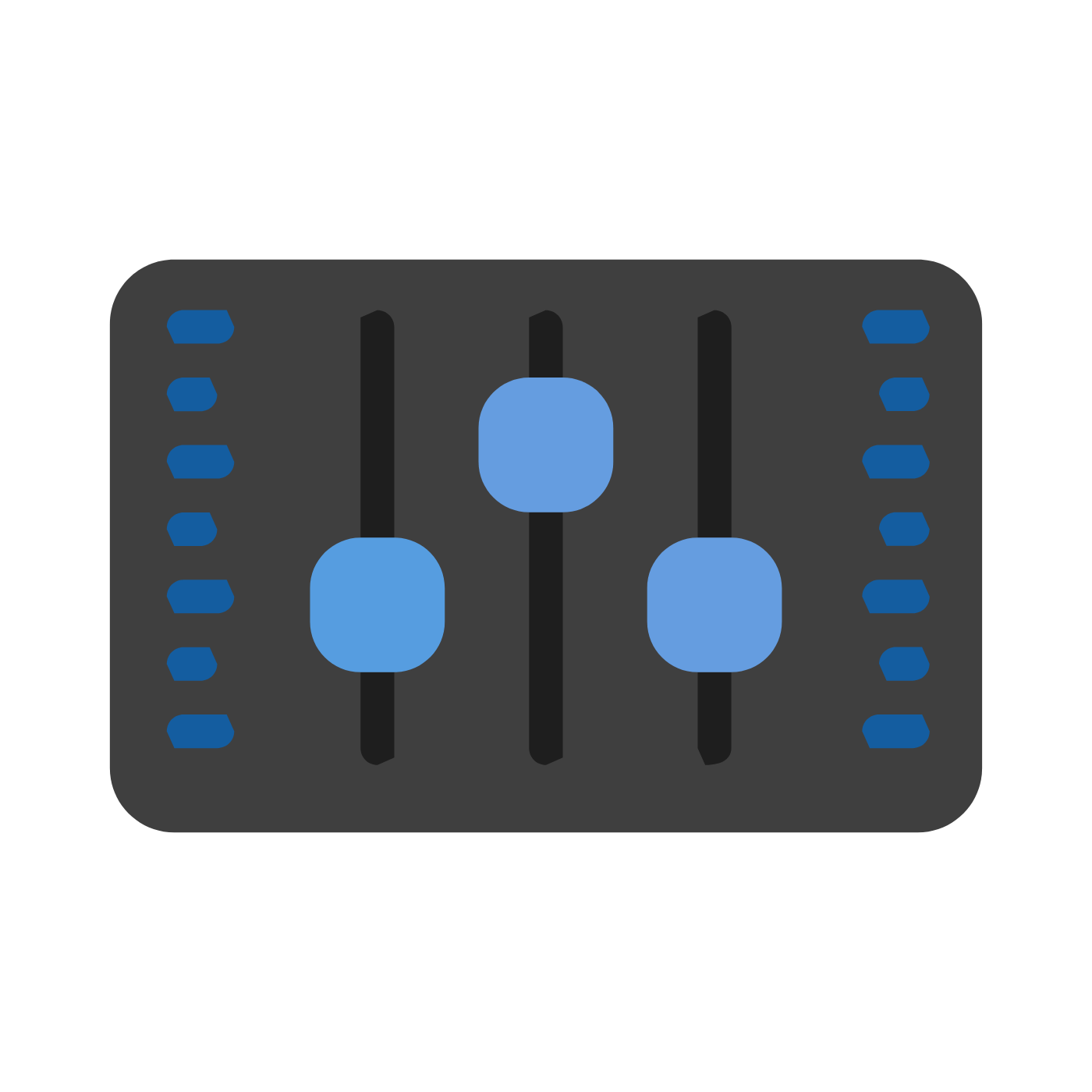
No-Support 3D Printing
Typically, support structures are necessary in LPBF processes to prevent the deformation of parts due to high temperatures and to anchor the build to the substrate.
However, no-support LPBF printing can offer several distinct advantages, such as material efficiency, reduced post-processing, and faster build times.
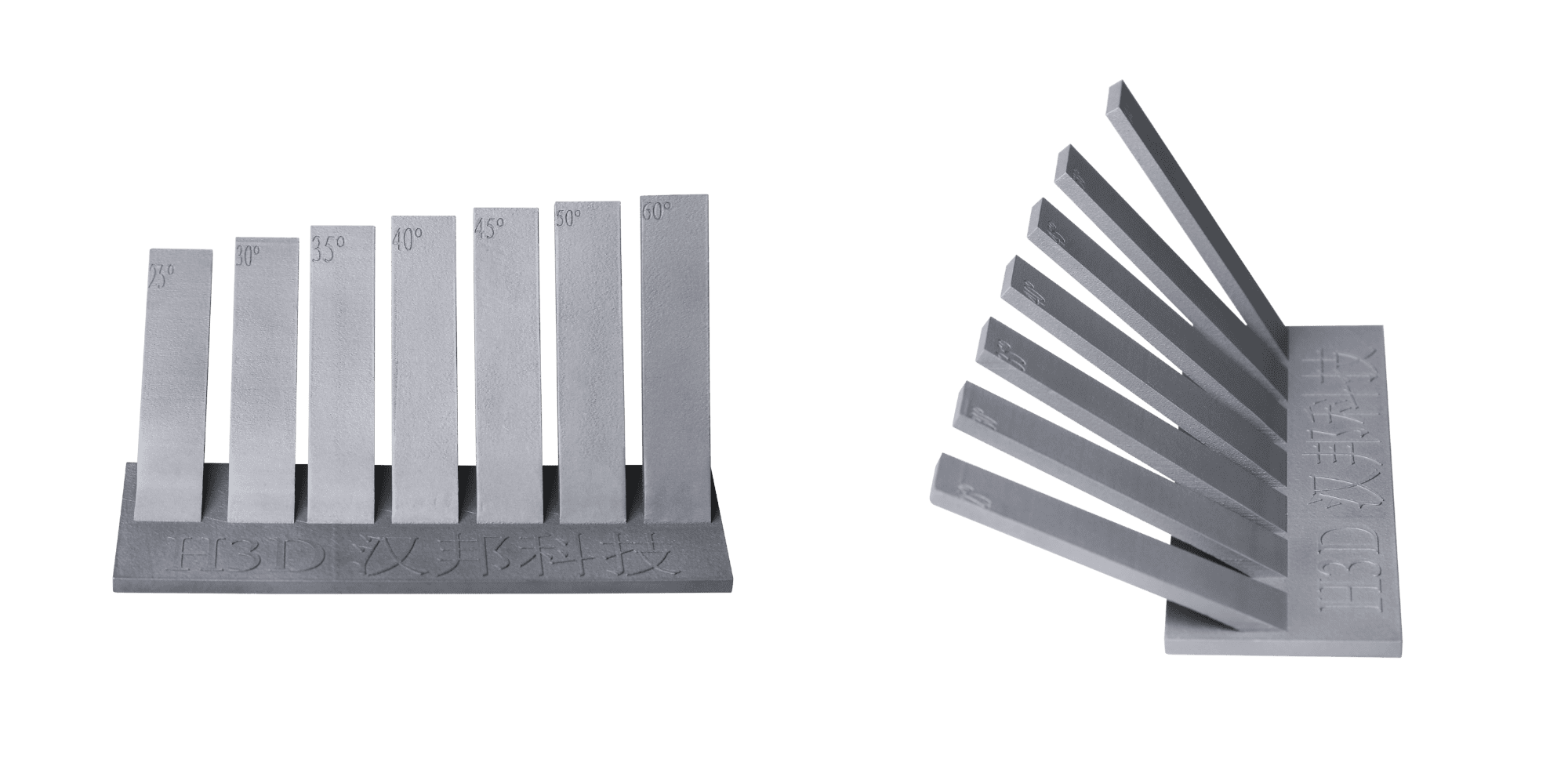
Application Experience
HBD's research center constantly works on process and application development for no-support 3D printing, achieving successful prints with support angles below 45°.
Common Applications
HBD Series
Compare with similar 3D printers.
Each HBD 3B printer offers distinct build plate sizes and laser configurations tailored to your specific part sizes, materials, and production volumes. Contact us to choose the model that best suits your business needs.
Request a Quote350 x 400 x 400 mm
430 x 520 x 520 mm
660 x 660 x 1,250 mm
2 x 500 W (IPG), 6 x 500 W (Standard), 6 x 1000 W (IPG)
2 x 500 W (IPG), 3 x 500 W (IPG), 3 x 1000 W (IPG)
8 x 500 W (IPG), 8 x 1000 W (IPG)
±0.05-0.20 mm
±0.05-0.20 mm
±0.05-0.20 mm
20-120 μm
20-120 μm
20-120 μm
70-200 μm
70-200 μm
70-200 μm
Compatible Materials
HBD metal 3D printers are open-material systems and compatible with an extensive catalog of third-party metal powders, ranging from stainless steels to titanium-based alloys, and tool steels. This section only lists the compatible metal powders customized by HBD.
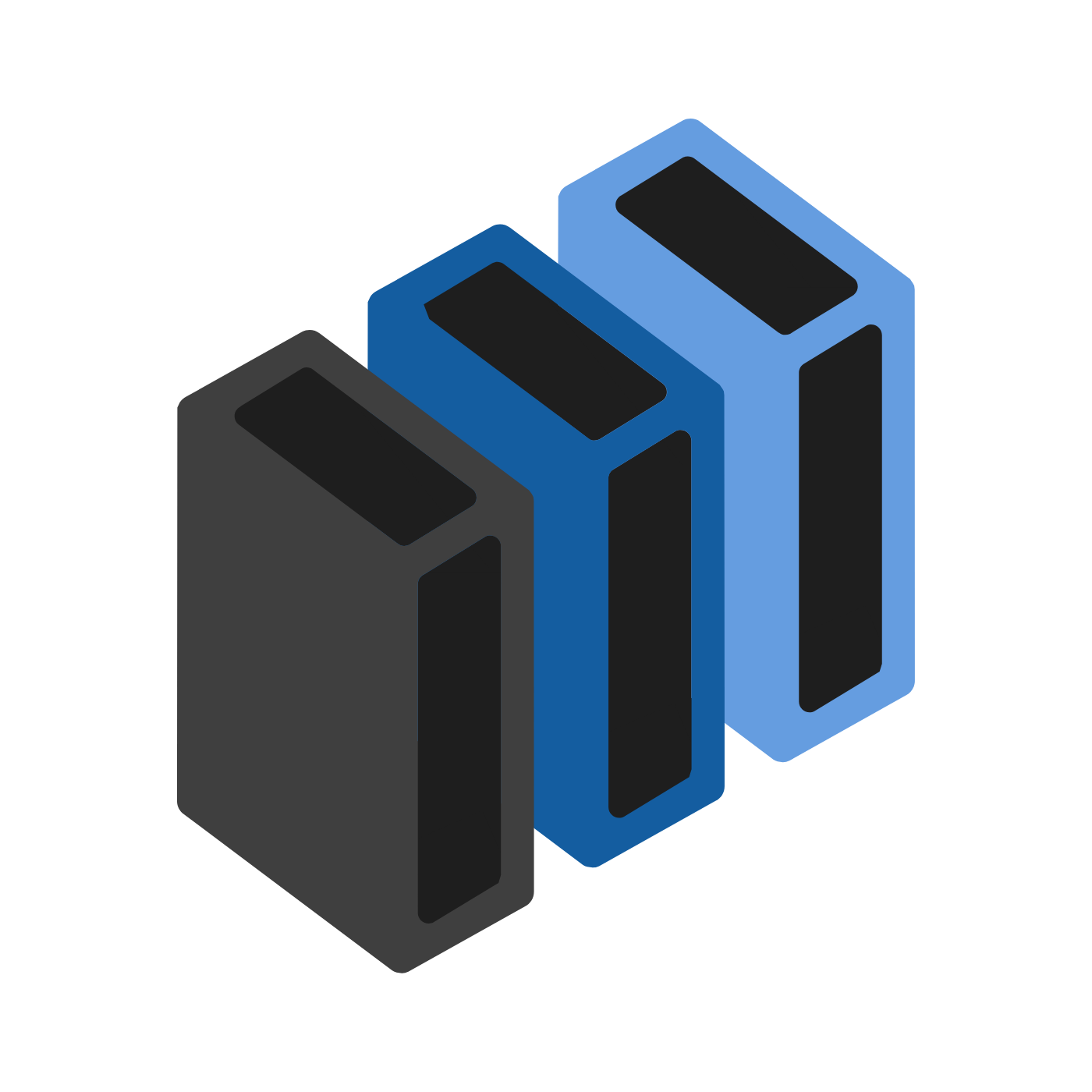
Stainless Steels
HBD 316L Stainless Steel, HBD 17-4 PH Stainless Steel, HBD 15-5 PH Stainless Steel
Tool Steels
HBD 420 Tool Steel, HBD CX Tool Steel
Aluminum-Based Alloys
HBD AlSi10Mg Aluminum Alloy
Titanium-Based Alloys
HBD TC4 Titanium Alloy, HBD TA15 Titanium Alloy
Cobalt-Based Alloys
HBD CoCrMo Cobalt Alloy
Maraging Steels
HBD 18Ni300 Maraging Steel
Copper-Based Alloys
HBD CuCrZr Copper Alloy
Tungsten
HBD W Tungsten
Superalloys
HBD IN625 Superalloy, HBD IN718 Superalloy, HBD GH99 Superalloy, HBD GH230 Superalloy, HBD Hastelloy X Superalloy
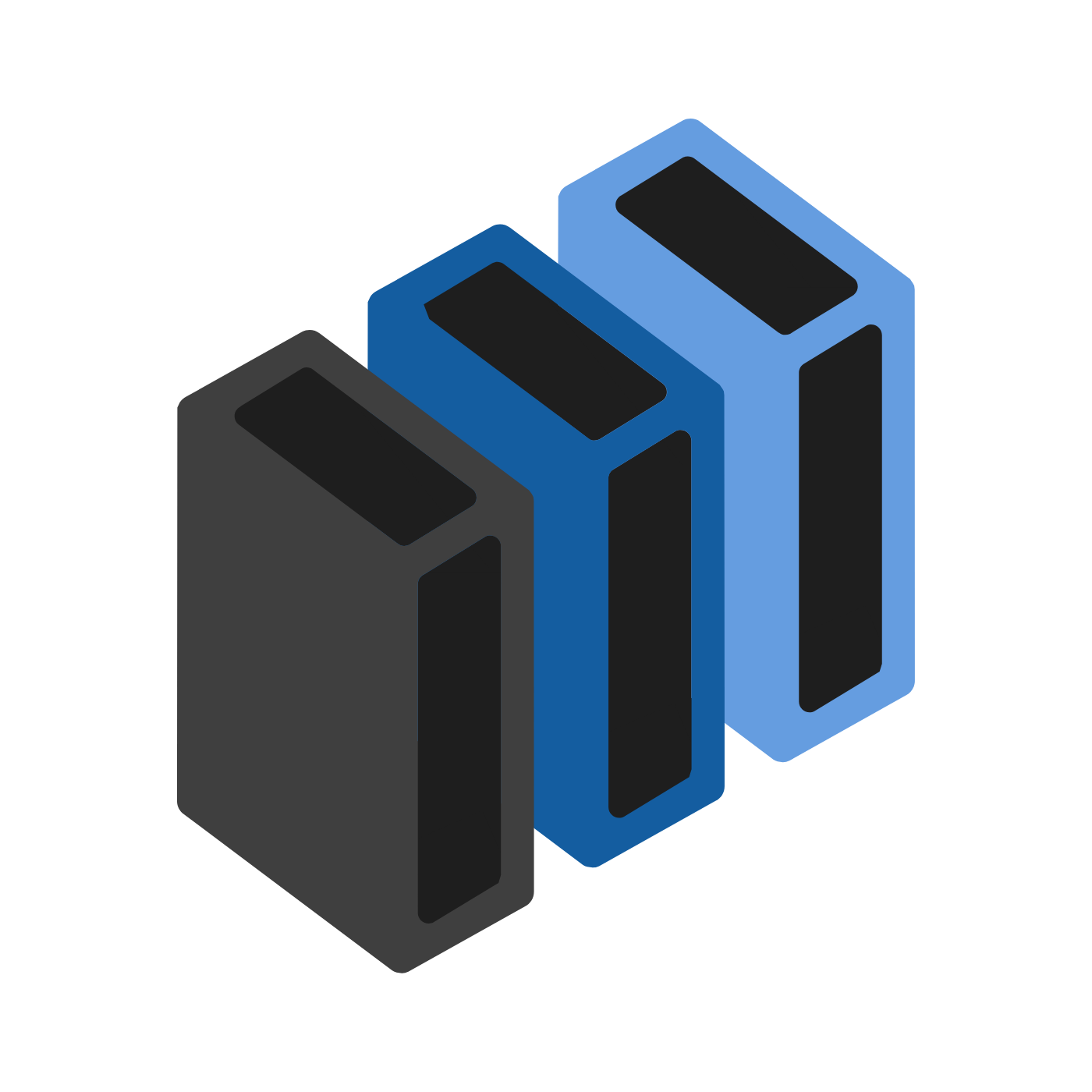
Links and Documents
Check out HBD's relevant resources for LPBF printers.
Links and Documents
Check out HBD's relevant resources for LPBF printers.